When choosing a lathe chuck, the 3-jaw and 4-jaw lathe chucks are the most common options. This article will delve into the common applications, main differences, and maintenance and care methods for these two types of chucks to help you make the best choice.
3 Jaw Lathe Chuck vs. 4 Jaw Lathe Chuck Common Applications
3 Jaw Lathe Chuck:The 3-jaw lathe chuck is typically used for machining round workpieces. Since its three jaws simultaneously grip the workpiece and automatically center it, it is particularly suitable for tasks that require quick setup and high efficiency. Common applications include:
- Turning round bars
- Machining pipes
- Precision machining of round parts
4 Jaw Lathe Chuck:The 4-jaw lathe chuck is more versatile and suitable for various shapes of workpieces, including irregularly shaped ones. Each jaw can be adjusted independently, making it very useful in situations that require precise gripping and centering. Common applications include:
- Machining square or rectangular workpieces
- Gripping irregularly shaped parts
- High-precision machining that requires accurate centering
3 Jaw Lathe Chuck vs. 4 Jaw Lathe Chuck Main Differences
Gripping Method
– 3 Jaw Lathe Chuck: Three jaws grip the workpiece simultaneously, automatically centering it.
– 4 Jaw Lathe Chuck: Each jaw can be adjusted independently, which is suitable for irregularly shaped workpieces.
Setup Time
– 3 Jaw Lathe Chuck: Quick setup, ideal for mass production.
– 4 Jaw Lathe Chuck: Longer setup time, but more flexible gripping.
Precision
– 3 Jaw Lathe Chuck: High centering precision, but suitable for round workpieces.
– 4 Jaw Lathe Chuck: Can achieve higher gripping precision, suitable for various shapes of workpieces.
3 Jaw Lathe Chuck vs. 4 Jaw Lathe Chuck Maintenance and Care
-3 Jaw Lathe Chuck
Regular Cleaning: Use compressed air or a brush to remove metal chips and dust from the chuck.
Lubrication: Regularly lubricate the moving parts of the chuck to keep it flexible.
Wear Inspection: Regularly check the wear condition of the jaws and replace them if necessary.
-4 Jaw Lathe Chuck
Cleaning: Similar to the 3-jaw lathe chuck, regularly remove metal chips and dust.
Lubrication: Each jaw needs to be lubricated individually to ensure smooth movement.
Adjustment and Calibration: Since each jaw can be adjusted independently, regular calibration is necessary to ensure gripping precision.
Autogrip Machinery is a leading power chuck, collet chucks, and rotary cylinders manufacturer in Taiwan. Maximize your machining efficiency and accuracy with Autogrip Machinery’s high-quality 3-jaw and 4-jaw chucks. We understand that the right chuck is essential for achieving optimal results, and Autogrip Machinery’s comprehensive range is designed to meet the demands of any application.
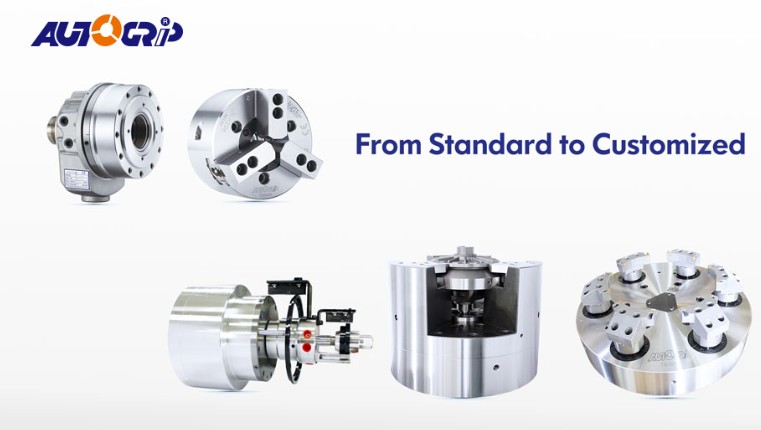
Autogrip Machinery’s 3 jaw lathe chucks are the ideal choice for high-volume production of round parts. Their quick setup and automatic centering ensure consistent results and minimize downtime, maximizing your productivity.
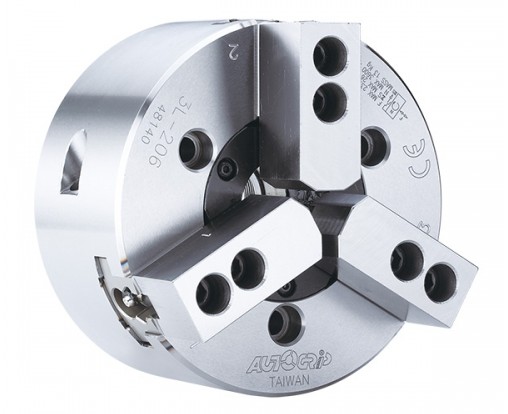
For machining irregular shapes, Autogrip Machinery’s 4 jaw lathe chucks offer unparalleled flexibility. Each jaw can be adjusted independently, allowing you to achieve precise gripping and centering for even the most complex workpieces.
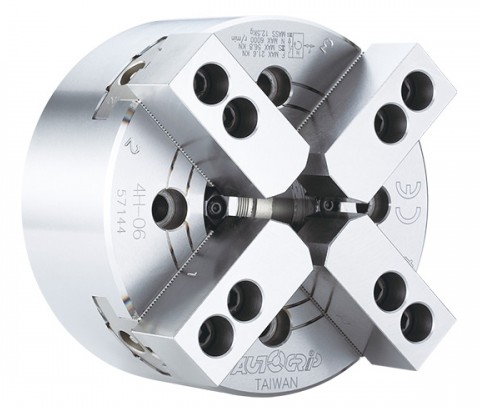
Ready to elevate your machining capabilities?
Contact Autogrip Machinery today to discuss your needs and discover the perfect lathe chuck for your application.