Computer Numerical Control (CNC) lathes have revolutionized the manufacturing industry by providing precision, efficiency, and versatility in machining operations. Among the various types of CNC lathes, slant bed and flat bed configurations are widely used, each offering distinct advantages and suited for different applications. This report delves into the differences between slant bed CNC lathes and flat bed CNC lathes, providing a comprehensive analysis based on structural design, performance, applications, and other critical factors.
Structural Design
Slant Bed CNC Lathe
The slant bed CNC lathe is characterized by its inclined bed design, where the plane of the guide rails intersects the ground at angles typically ranging from 30° to 75° (Smart Lathe). This configuration forms a right-angle triangle when viewed from the side, allowing for longer X-direction travel and more tool alignments. The inclined design facilitates gravity-assisted chip removal, which enhances machining efficiency and reduces the risk of tool interference (HCNC Group).
Flat Bed CNC Lathe
In contrast, the flat bed CNC lathe features a horizontal, flat bed where the guide rails are parallel to the ground. This design provides a stable and robust platform, making it suitable for handling large or irregularly shaped workpieces. The flat surface allows for easy mounting and alignment of workpieces, which is beneficial for certain types of operations (Blin Machinery).
Performance and Machining Capabilities
Cutting Rigidity and Vibration
The slant bed CNC lathe boasts a larger cross-sectional area compared to the flat bed, providing greater mechanical resistance to bending and torsion. This results in higher rigidity and stability during machining operations. The cutting force in a slant bed lathe aligns with the direction of gravity, allowing the spindle to run more smoothly and reducing the likelihood of turning vibrations (STS CNC).
Conversely, the flat bed CNC lathe experiences cutting forces at a 90° angle to the gravity of the workpiece, which can lead to increased vibration and potential machining inaccuracies. However, the flat bed’s stability makes it well-suited for heavy-duty operations and machining larger parts (Machining Concepts).
Machining Accuracy and Repeatability
Slant bed CNC lathes are often equipped with high-precision components such as linear guideways and ball screws, enhancing their accuracy and repeatability. These features make slant bed lathes ideal for precision tasks and complex operations, commonly found in industries like automotive, aerospace, and electronics (Yash Machine).
Flat bed CNC lathes, while offering a stable platform, may not provide the same level of rigidity and precision as slant bed machines. However, their durability and ability to handle a wide range of materials and operations make them versatile for various applications (Bhavya Machine Tools).
Applications and Suitability
Slant Bed CNC Lathe
Slant bed CNC lathes are particularly suited for high-volume production runs and applications that demand consistent quality and efficiency. Their ergonomic design allows for easier access and faster setup changes, enhancing operator comfort and productivity. These lathes are widely used in industries requiring precision and reliability, such as automotive and aerospace (Blin Machinery).
Flat Bed CNC Lathe
Flat bed CNC lathes are renowned for their versatility and are commonly found in job shops and repair shops where flexibility is more critical than high-volume production. They are well-suited for tasks involving large or irregularly shaped workpieces and can handle a wide range of materials and operations. The flat bed’s stability makes it ideal for machining larger parts or conducting heavy-duty operations (HCNC Group).
Economic and Operational Considerations
Cost and Maintenance
The choice between slant bed and flat bed CNC lathes often depends on budgetary constraints and specific machining needs. Slant bed lathes, with their advanced features and precision capabilities, may come at a higher initial cost but offer long-term benefits in terms of efficiency and quality. Maintenance requirements for slant bed lathes may also be higher due to their complex design and components (Machining Concepts).
Flat bed lathes, on the other hand, are generally more affordable and require less maintenance due to their simpler design. They offer a cost-effective solution for operations that do not require the high precision and speed of slant bed lathes (Bhavya Machine Tools).
Conclusion
In conclusion, the choice between slant bed and flat bed CNC lathes hinges on several factors, including machining requirements, production volume, budget, and specific application needs. Slant bed CNC lathes offer superior rigidity, precision, and efficiency, making them ideal for high-volume production and precision tasks. Flat bed CNC lathes, with their stability and versatility, are better suited for handling larger workpieces and a broader range of operations.
Understanding the distinct advantages and limitations of each type of CNC lathe allows manufacturers to make informed decisions that align with their production goals and operational needs. By selecting the appropriate CNC lathe, businesses can enhance their manufacturing capabilities, improve efficiency, and drive profitability.
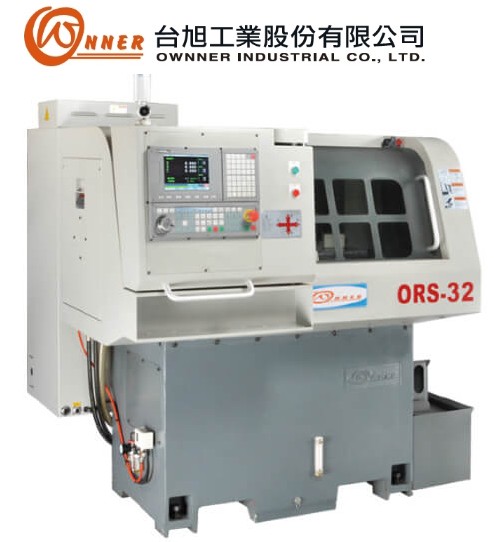
OWNNER INDUSTRIAL CO., LTD. is a renowned manufacturer specializing in high-quality CNC turning centers, offering innovative solutions tailored to meet the diverse needs of the machining industry. Among their flagship products are the flat bed CNC lathes and slant bed CNC lathes, both designed to enhance precision and efficiency in manufacturing processes.
The flat bed CNC lathe is celebrated for its robust design, making it ideal for heavy-duty operations and large workpieces.Its gang tooling system allows for quick tool changes, enabling versatility across various applications, including precision parts and mechanical components. Meanwhile, the slant bed CNC lathe features an inclined design that optimizes chip removal and enhances machining accuracy, making it perfect for high-volume production of intricate parts in industries such as aerospace and automotive. At OWNNER, they are committed to providing cutting-edge technology that drives productivity and quality in manufacturing. For more information about OWNNER’s products, contact them today!