Magnetic drive pumps, also known as mag-drive pumps, are a fascinating piece of engineering in the industrial world. They operate without traditional mechanical seals, using magnetic coupling instead to transfer power from the motor to the impeller. This unique design offers several advantages but also comes with some limitations that make them suitable for specific applications.
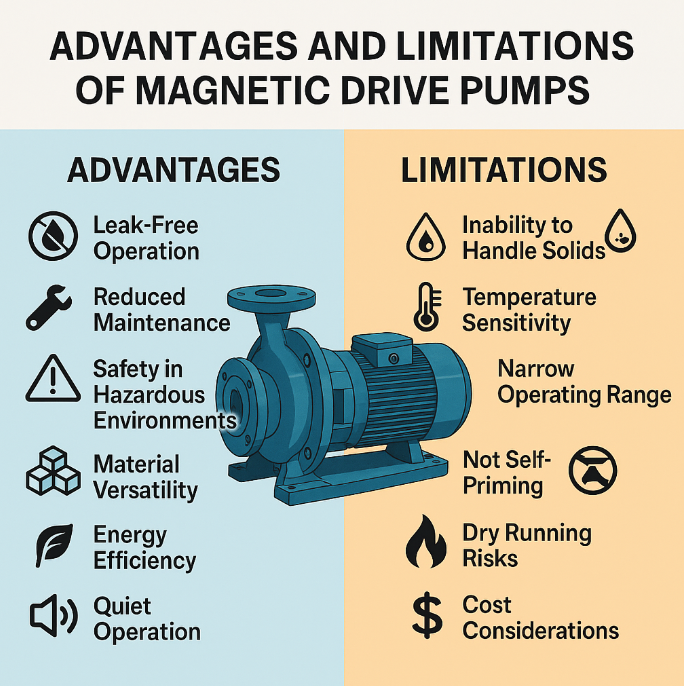
Advantages of Magnetic Drive Pumps
- Leak-Free Operation: One of the most celebrated features is their seal-less design. By eliminating mechanical seals, these pumps significantly reduce the risk of leaks. This makes them ideal for handling hazardous or toxic fluids like acids and alkalis.
- Reduced Maintenance: Without seals, there’s no need to worry about wear and tear on these components, which are often a source of pump failure in traditional designs.
- Safety in Hazardous Environments: These pumps excel in environments where leakage could pose severe risks—think chemical plants or pharmaceutical facilities dealing with corrosive or flammable substances.
- Material Versatility: Available in both metallic and non-metallic materials, mag-drive pumps can be tailored to withstand different chemical properties and temperatures.
- Energy Efficiency: The absence of a direct mechanical connection minimizes energy loss due to friction, making these pumps more efficient than some alternatives.
- Quiet Operation: Their design inherently reduces noise levels compared to other pump types.
Limitations of Magnetic Drive Pumps
- Inability to Handle Solids: Mag-drive pumps struggle with liquids containing solids or particulates. These can clog the tight tolerances within the pump, leading to performance issues or even failures.
- Temperature Sensitivity: The magnets used in these pumps can lose their magnetism if exposed to high temperatures beyond their threshold, limiting their use in certain applications.
- Narrow Operating Range: Like centrifugal pumps, they have an optimal efficiency point and operating range. Deviating from this range can lead to inefficiencies and potential damage.
- Not Self-Priming: Most mag-drive pumps require priming before operation since they can’t handle air pockets effectively.
- Dry Running Risks: Since the pumped liquid acts as both lubricant and coolant for internal components, running dry can cause severe damage quickly—a major drawback for industries requiring continuous operation without constant monitoring.
- Cost Considerations: While offering long-term savings through reduced maintenance needs, their initial cost is higher compared to conventional sealed pumps.
- Power Limitations: Extremely high-power applications may not be feasible due to limitations in magnetic coupling strength and size constraints.
Applications Where They Shine
- Chemical processing plants
- Pharmaceutical manufacturing
- Food & beverage industries (for ultra-pure liquids)
- Semiconductor fabrication (handling sensitive chemicals)
Despite their drawbacks, magnetic drive pumps remain a go-to solution for industries prioritizing safety and leak prevention over broad operational flexibility or solid-handling capabilities.
For those considering mag-drive technology versus other options like electric diaphragm pumps or traditional centrifugal models? It’s all about weighing your specific needs against what each type brings—or doesn’t bring—to the table!
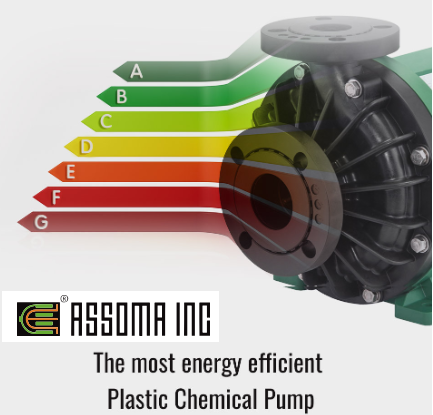
If you are looking for high-performance magnetic drive solutions, ASSOMA INC., one of Taiwan’s leading magnetic drive pump manufacturers, offers exceptional options. Their AVF-C Series canned motor pumps and AVF-X Series magnetically driven centrifugal pumps have earned prestigious accolades, including the 2023 Taiwan Excellence Award for their energy efficiency, leak-free reliability, and ability to meet or exceed stringent EU energy standards. These award-winning models are trusted across critical industries for promoting safe, sustainable, and maintenance-friendly operations.
Browse ASSOMA’s full range of chemical transfer pump solutions and find the right model to optimize your fluid handling systems today.