To know more about injection molding? In addition to the basic introduction to injection molding, this article also analyzes the advantages, disadvantages, and application scope of injection molding. The most important thing is that this article teaches you how to save injection molding costs for your company. If you are facing whether to use injection molding process production, you must read it.
1. What is injection molding?
Injection molding instructions:
Injection molding is the most commonly used process for producing plastic parts which are mainly accomplished by melting plastic at high temperature and injecting it into a mold. The plastic injection molding process is suitable for mass production of the same plastic product in a short period of time.
Common materials for injection molding:
Injection molding materials include thermoplastic, thermoset plastic, elastomer, or metal-based materials, and the most commonly used are thermoplastic and thermoset polymers. High-performance plastics that can withstand high temperatures are gradually replacing traditional plastics.
2. What are the steps of injection molding?
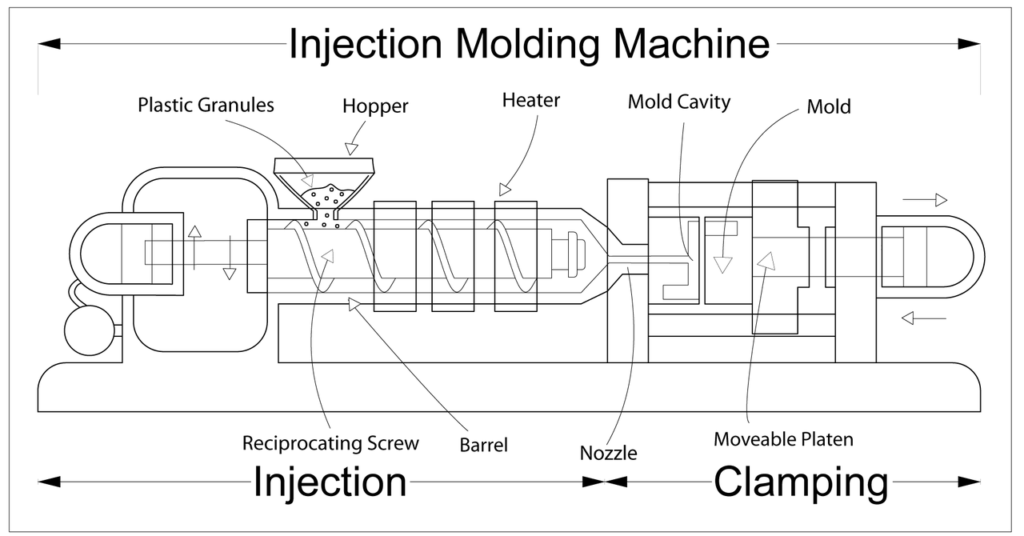
Image from:https://easchangesystems.com/application/plastic-injection-molding/
1. Plasticization
The plastic material of injection molding is usually granular, which needs to be heated at a high temperature so that the raw materials can melt in the material tube.
2. Injection Filling
The heated plastic is filled into the mold through the screw.
3. Pressurization
In order to avoid the backflow of the raw material, when the raw material is filled into the mold, the space in the mold will continuously be pressurized to ensure the compactness of the raw material filling.
4. Cooling
After the mold is filled, the injection part needs to cool down, and the cooling time depends on the type of plastic used and the thickness of the part. Each mold is designed with internal cooling or heating lines, and water circulates through the mold to maintain a constant temperature.
5. Ejection
After cooling down the mold, the ejector pin on the mold will push the product out of the mold.
3. What is the applicable scope of injection molding?
The application range of injection molding can be mainly divided into six categories:
1. Food and Beverage:
When it comes to injection molding, the food and beverage industry relies on plastic materials to manufacture product packaging and containers, and different types of injection-molded food containers such as plastic cookie mold. So, components used in food and beverage processing equipment must meet safety guidelines including BPA-free, FDA-certified, non-toxic, and GMA safety regulations.
2. Auto parts:
Many parts of modern automobiles have turned to plastic injection molding for development, planning, and manufacturing. Auto parts by automotive injection mold technique, plastic injection molding to accomplish through standardization and modularization, the development of molds can be more cost-effective, and automobile parts can also be produced more quickly and consistently.
3. Medical and pharmaceutical:
Because many medical products must be shatterproof, non-porous, and perfectly shaped, medical plastic injection molding is critical for medical and pharmaceutical production. As a high-volume producer, the medical industry can benefit from the reduced production time and affordable production materials of injection molding, while still obtaining high-quality medical-grade products. Medical and pharmaceutical parts manufactured using injection molding range from medicine bottles to X-ray assemblies.
4. Household items:
With a simple trip to your kitchen, you have a good chance of finding household injection moldings or parts. From Tupperware to building materials used in construction, there’s no denying the industry wouldn’t be what it is today without injection molding. Through the production method of plastic household mold molding, household products can be made more affordable and more diverse.
5. Agriculture:
The choice of reinforced plastics is favored due to new plastic material properties such as UV resistance, impact resistance, moisture resistance, etc. The ability to produce durable products that can stand up to the elements of the farm makes plastic injection molding clearly suitable for agriculture, from feeding troughs to specialized harvesting components.
6. Electronic products:
While many people think of electronic components as metal mechanical parts that run primarily on electricity, improving system longevity with a corrosion-resistant plastic enclosure improves overall performance. As you might have guessed, manufacturing the case via a plastic electronic injection molding process is preferred. The computer mouse you’re probably using right now, as well as the TV in your living room, probably has some components that are injection molded from plastic.
4. what are the advantages and disadvantages of injection molding?
advantage:
1. Low Scrap Rates with Injection Molding
Injection molding produces lower scrap rates compared to traditional manufacturing processes such as CNC machining, which cut away most of the original plastic block or sheet.
2. Each product is Consistency
Injection molding ensures consistency in every part produced, as one of the characteristics of plastic injection molding.
Drawbacks:
1. Small design errors will cause big costs with injection molding
The early stage of development costs a lot because of testing, tooling requirements, and the mass-produced parts quantity requirement from the manufacturer. All you need to do is to make sure you get the design right the first time.
2. Be Ready for High Tooling Costs for Injection Molding
When you develop a mold up front, you have to design the part and make a prototype, you have to design a mold that can mass-produce replicas of the part and make a prototype. Finally, after extensive testing in the two stages above, you can inject mold apart. However, you need to be ready It might cost more money in the process.
5. How to save the cost of injection molding for yourself?
1. Consider the injection part size
The amount of material should be reduced as much as possible, cause unnecessarily large parts or features add not only a monetary cost but also a time cost.
2. Design for manufacturability analysis
Finding an experienced partner or mold maker can save you a lot of time and money in the long run. Identifying issues such as impossible geometries, insufficient draft angles, and moldable features at an early stage will eliminate financial and cosmetic expenses along the way.
3. Intelligent mold design
You can save money by partnering with a molder who designs molds intelligently. How your part is positioned in the mold can have a major impact on cost. Correct part positioning optimizes how molds are filled and reduces scrap.
4. Modify your mold
Reduce costs by modifying molds rather than buying a brand-new mold for every modification. With design tool inserts, you can shape various versions and functions.