In the fast-paced world of industrial packaging, efficiency, accuracy, and cost-effectiveness are paramount. Automatic weighing and bagging machines have emerged as critical tools in achieving these goals. These machines streamline the packaging process by automating the filling, sealing, and labeling of products into bags, significantly reducing the need for manual labor. This report delves into the intricacies of automatic weighing and bagging machines, exploring their working mechanisms, types, benefits, and applications across various industries.
What is an Automatic Weighing and Bagging Machine?
An automatic weighing and bagging machine is an industrial device designed to package bulk materials or products into bags or containers with minimal human intervention. These machines are indispensable in industries that require the packaging of large volumes of items quickly and accurately. They are equipped with advanced technology, including sensors and control systems, to measure and monitor the weight of the product being packaged. Once the desired weight is achieved, the machine automatically dispenses the product into the packaging material, ensuring uniformity and precision.
Core Functions
- Filling: The primary function of these machines is to fill bags with the correct amount of product. This can range from powders and granules to liquids and solid items. Automated bagging machines use sensors and conveyors to ensure each bag receives the exact quantity needed.
- Sealing: Once filled, the machine seals the bag to protect its contents. Sealing can be done through various methods such as heat sealing, ultrasonic sealing, or adhesive sealing. This ensures the product remains intact and uncontaminated during transport and storage.
- Labeling: Many automatic bagging systems also feature integrated label printers, enabling businesses to include shipping addresses, barcodes, and other product information on each bag. This eliminates the need for manual labeling and further enhances efficiency.
Types of Automatic Weighing and Bagging Machines
Automatic weighing and bagging machines come in various types, each suited to different levels of production and automation needs. The three main types are manual, semi-automatic, and fully-automatic machines.
Manual Bagging Machines
Manual bagging machines are the simplest type. They require an operator to manually place the bags and control the filling process. These machines are ideal for small-scale operations or for packaging lightweight materials.
Semi-Automatic Bagging Machines
Semi-automatic bagging machines offer a balance between manual and fully-automatic systems. They still require some human intervention but use mechanical systems to assist with the filling and sealing process. An operator typically places the bag, and the machine handles the rest.
Fully-Automatic Bagging Machines
Fully-automatic bagging machines are the most advanced and efficient. These machines handle everything from bag placement to filling, sealing, and even labeling. They use sensors, conveyor belts, and other automated systems to ensure high accuracy and speed.
Advantages of Automatic Weighing and Bagging Machines
Automatic weighing and bagging machines offer several advantages that make them essential tools in modern packaging operations.
Increased Efficiency
Automated systems fill and seal bags much faster than manual methods. For instance, the AUTOBAG® Brand PaceSetter PS 125™ Tabletop Baggers can bag and seal up to 80 bags per minute. This speed can be a game-changer for businesses that need to package large quantities of materials quickly.
Improved Accuracy
One of the standout features of automated bagging machines is their ability to dispense precise quantities of materials. This is crucial for businesses that need to adhere to specific weight or volume requirements.
Reduced Labor Costs
By automating the packaging process, businesses can significantly reduce labor costs. These machines eliminate the need for manual weighing, measuring, and packaging, allowing companies to reallocate their workforce to more value-added tasks.
Enhanced Safety
Safety is a critical consideration in any packaging operation. Automated bagging machines can reduce the risk of injury to workers by eliminating the need for manual handling of heavy or awkward materials.
Customization and Flexibility
These machines are highly customizable, allowing companies to switch between different bag sizes and products seamlessly. This is particularly advantageous for industries that need to handle a variety of products. Furthermore, many systems come with additional features such as automated label printing, integrated weighing scales, and the ability to print marketing materials directly on the bags.
Applications Across Industries
Automatic weighing and bagging machines are used in various sectors such as the food, medical, pharmaceutical, and e-commerce industries. They are versatile technologies that can accommodate a wide range of materials, including granular, powders, and liquids.
Food Industry
In the food industry, these machines ensure precise and hygienic packaging of products like snacks, powdered goods, and liquids. They help maintain product safety and quality by reducing the risk of contamination and ensuring consistent portion sizes.
Pharmaceutical Industry
Precision is crucial in the pharmaceutical industry, where adhering to specific weights and measurements is of utmost importance. Automatic weighing and packing machines guarantee precise and uniform packaging, reducing the likelihood of errors and customer dissatisfaction.
E-commerce Industry
In e-commerce, where large volumes of items need to be packaged quickly and accurately, automated bagging machines streamline operations by handling everything from filling and sealing to printing labels. This allows workers to focus on other tasks, significantly increasing throughput and accuracy.
Conclusion
Automatic weighing and bagging machines have revolutionized the packaging industry, providing businesses with a key tool for success. From improving efficiency and accuracy to customization and enhanced product safety, these machines offer a range of benefits that cannot be achieved through manual packaging processes. As the demand for fast, precise, and reliable packaging solutions continues to grow, automatic weighing and bagging machines will remain at the forefront of packaging success.
If you require automatic weighing and bagging machines, don’t miss out on CTI Machine – a professional packaging machine manufacturer in Taiwan. They deliver cutting-edge solutions that offer unmatched precision and efficiency across industries such as agriculture, food, and pharmaceuticals. In addition to their automatic weighing and bagging machines, they provide a range of machines, including vertical vacuum packing machines and premade pouch packaging machine solutions. Their advanced technology will make your production line more efficient and reliable. Visit CTI Machine’s website to enhance your packaging operations with their customizable, high-performance equipment.
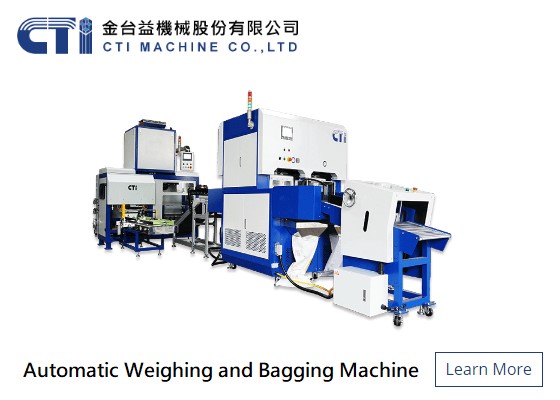